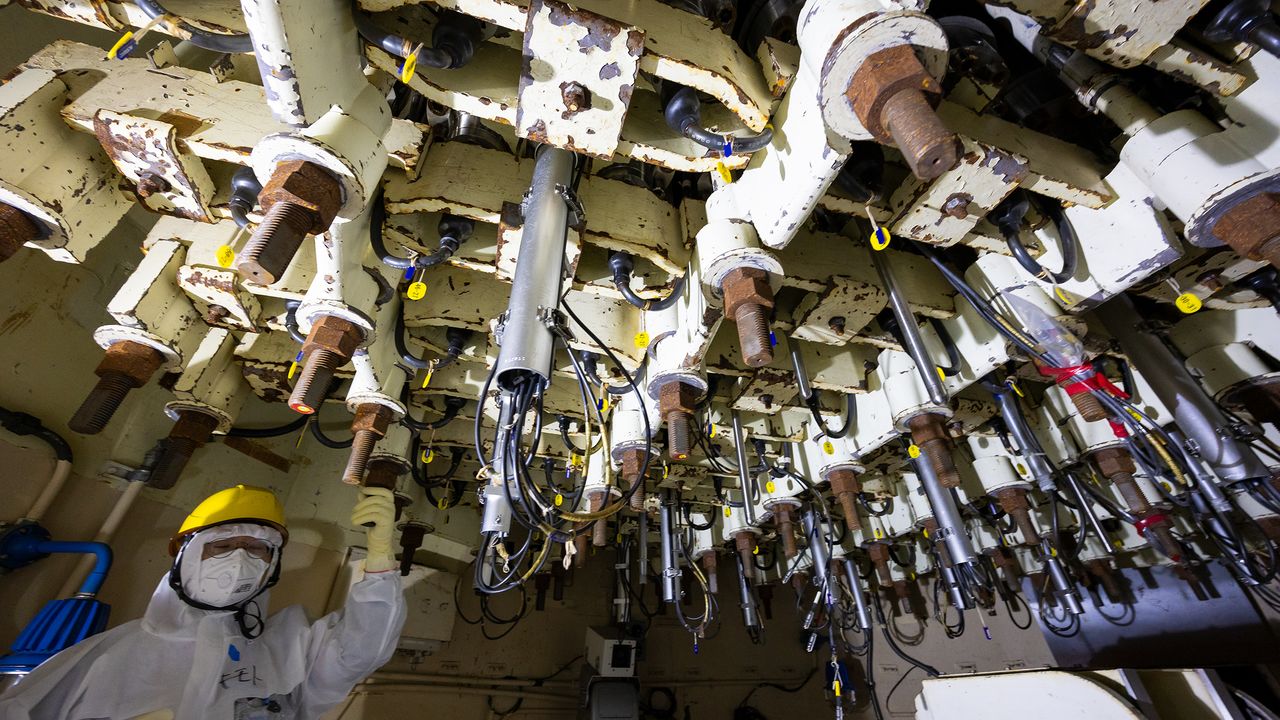
The First Small Steps: Debris Removal at Fukushima Daiichi
Society Economy Disaster- English
- 日本語
- 简体字
- 繁體字
- Français
- Español
- العربية
- Русский
In November 2024, TEPCO, the Tokyo Electric Power Company, successfully removed approximately 0.7 grams of fuel rod debris from the Unit 2 reactor at the stricken Fukushima Daiichi Nuclear Power Station in a November 2024 trial operation. The trial, initially scheduled for 2021, was delayed due to the time taken to build recovery equipment and make other preparations. To understand just how the workers managed to remove the debris, we went inside the Unit 5 reactor, which has more or less the same design as the stricken Unit 2 reactor. At the time of the tsunami, the Unit 5 reactor was shut down for scheduled maintenance, which is why it managed to escape serious damage. This relatively unharmed structure has proved useful as full-scale simulator that can be used in the development of recovery systems and the selection of the routes by which robots are deployed into the Unit 2 reactor.
Units 5 (left) and 6 are built on a high-lying coastal area in the town of Futaba, to the north of the other four reactors. (© Hashino Yukinori)
Under the Pressure Vessel
Directly below the pressure vessel of the Unit 5 reactor, a battery of equipment, including devices to drive the control rods that regulate reactor output, hang down in close proximity, like icicles. A long shaft known as the “X-6 penetration,” which is normally used when replacing this equipment, serves as an entrance through which recovery equipment can approach the containment vessel.
This space is used to perform maintenance on the control rod drive systems and other apparatus that hang from the Unit 5 pressure vessel. (© Hashino Yukinori)
The “X-6 penetration” conduit is visible at the bottom of this photo, taken in the corridor encircling the containment vessel. (© Hashino Yukinori)
The “X-6 penetration” shaft with its hatch open. Stowed machinery is visible inside. The white semicircular area beyond that is the interior of the containment vessel. (© Hashino Yukinori)
The semicircle on the wall at right is the penetration conduit, as seen from the inside of the containment vessel. (© Hashino Yukinori)
Fishing for Debris
The X-6 penetration is 55 centimeters in diameter. In the November 2024 trial at Unit 2, workers inserted a guide pipe through this shaft, through which they passed a long contraption into the containment vessel, much like extending a fishing rod. From the tip of the rod, they then lowered a claw-like device through a gap in the grating, with which they retrieved a 0.7-gram sample of debris.
Because it is of course not possible for humans to enter the highly contaminated Unit 2 reactor, after first performing repeated surveys, the task is performed remotely while monitoring the camera feed. When one looks through the grating in Unit 5, one can see the apparatus used to replace the drive mechanisms that operate the control rods. In Unit 2, it is believed that all this equipment was ripped out by the molten fuel rods and now lies at the bottom of the containment vessel. The task of removing the debris is unimaginably difficult.
The grate in the workspace under the Unit 5 pressure vessel. (© Hashino Yukinori)
The bottom of the pressure vessel under the grating. In the Unit 2 reactor, it is believed that the molten fuel rods that burned through the base of the pressure vessel ripped out the internal structure, creating a pool of debris. (© Hashino Yukinori)
A model of the Unit 2 reactor in the new main building of the Fukushima Daiichi Nuclear Power Station. The approach through the X-6 penetration and fuel rod debris are visible at bottom left. (© Hashino Yukinori)
A “Drop in the Ocean”
Ono Akira, CEO of the TEPCO Fukushima Daiichi Decontamination and Decommissioning Engineering Company, describes the autumn trial as a “drop in the ocean.”
“The first attempt might have only yielded a tiny drop of fuel. I believe that what is important, however, is that we can recover larger and larger quantities. We will be using the expertise gained through the trial for that purpose,” he explains.
Ono Akira, CEO of TEPCO’s Fukushima Daiichi Decontamination and Decommissioning Engineering Company. (Courtesy TEPCO Holdings)
Robot Arm Shows More Promise
TEPCO will also attempt a second trial retrieval in the spring of 2025. To reduce the challenges presented by the fishing-rod type device, which has an unstable tip, engineers are redesigning the tip, as well as making other improvements.
Immediately before last year’s recovery trial, engineers discovered that the pipe used to insert the retrieval device into the containment vessel had been assembled in the wrong order. To make things worse, the camera attached to the tip of the device also stopped working just before the tip gripped the debris.
“The task of connecting the pipes together in the correct order should have been an extremely simple one,” recalls Ono. “We therefore foresaw no safety issues. However, because this job was performed in a highly radioactive area where workers wear protective clothing and full masks, and had to be completed in a short time, workers had difficulty hearing each other and communicating.” Ono notes that during the next trial, TEPCO will exercise even greater caution, including with regard to tasks performed by workers.
By the end of March 2026, TEPCO also plans to commence another survey, this time using a robotic arm. Compared to the fishing-rod type apparatus, which effectively drops a line straight down through gaps in the grating, the robotic arm has a wider range of movement. Because the arm can also take radiation readings and capture footage at various points at the bottom of the containment vessel, it is hoped that it will be able to gather much more useful information in preparation for full-fledged debris recovery.
The total amount of contaminated debris in Units 1, 2, and 3 is estimated at 880 metric tons. Retrieving it all will be a long process, and there are likely to be unforeseen obstacles along the way.
Ono says, “In the past, we left training up to the contractors in charge of the decommissioning project. However, this is a difficult and unprecedented work environment, in which the required skills and knowledge are constantly changing. TEPCO has to play an active role in training its people, giving them the skills they need to take on this task. The decommissioning of a reactor is a long, all-hands-on-deck process. I’d like to see decommissioning performed in a sustainable fashion with involvement from local businesses as well.”
Units 1 to 3 seen from an observation deck: Around 880 tons of debris awaits collection. (© Hashino Yukinori)
(Originally written in Japanese by Kaida Naoe of Nippon.com. Banner photo: The interior of the containment vessel of Unit 5 at the Fukushima Daiichi Nuclear Power Station. Having more or less the same design as the melted-down Units 1 to 3, Unite 5 is used as a full-scale decommissioning simulator. © Hashino Yukinori.)