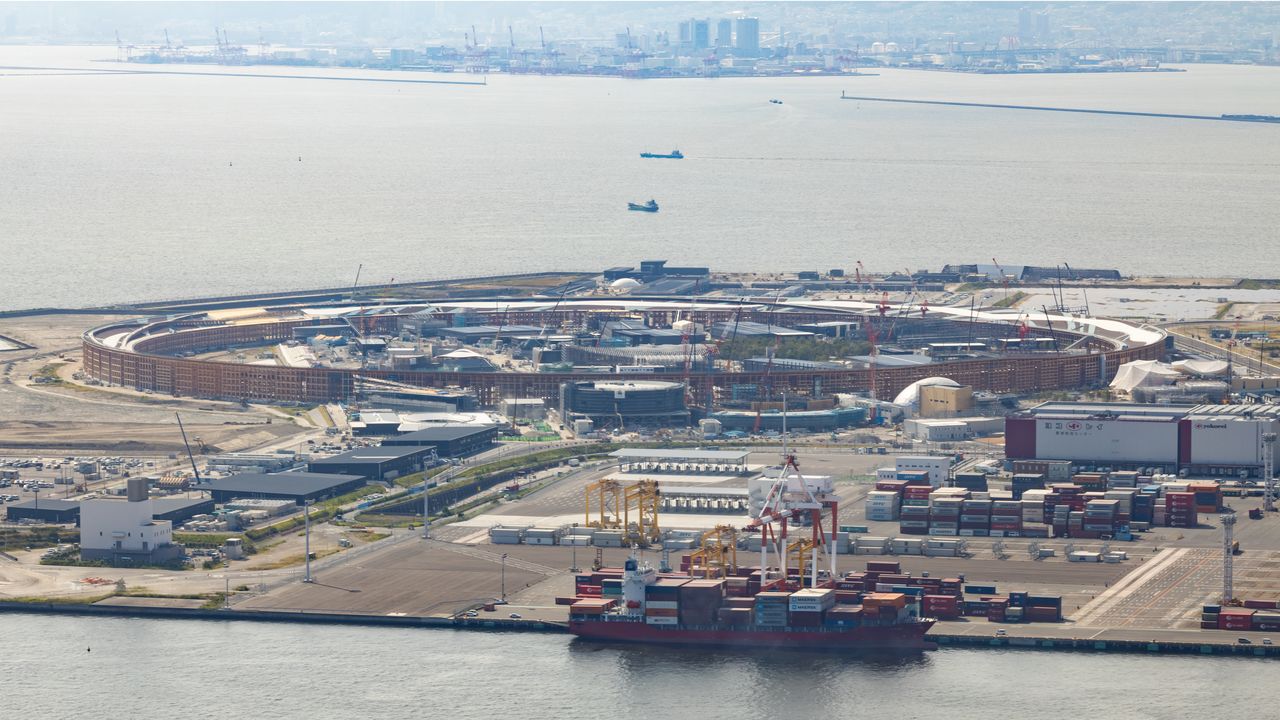
Spotlight on Hamadōri: the Fukushima Innovation Coast Framework
Osaka Expo’s Iconic Wooden Ring Features Fukushima Timber
Architecture Environment- English
- 日本語
- 简体字
- 繁體字
- Français
- Español
- العربية
- Русский
Osaka Expo to Showcase Fukushima Recovery
Work to construct the iconic wooden ring that surrounds the pavilions at Expo 2025, Osaka, Kansai finally finished in August 2024. At 20 meters high and 2 kilometers in circumference, the Grand Ring contains 27,000 cubic meters of wood, making it one of the largest wooden structures in the world.
The Grand Ring greets visitors to the pavilion area. (Courtesy Japan Association for the 2025 World Exposition)
Of this, 4,500 cubic meters of glued-laminated timber, or “glulam,” was supplied by Woodcore, a company based in Namie, Fukushima. The meltdown at the Fukushima Daiichi Nuclear Power Station triggered by the massive 2011 earthquake and tsunami hit the neighboring town hard, forcing all residents to evacuate. Since the partial lifting of evacuation orders for the area in 2017, Namie has begun to recover, although the town’s population has only recovered to 2,200—one tenth of what it was before the disaster.
Woodcore was established in 2018, in a partnership between Namie-based Asada Timber and Tōju Sangyō, a laminate manufacturer based in Kōriyama, also in Fukushima. A leading player in the recovery of the local agriculture, forestry, and fisheries sector, which the government-championed Fukushima Innovation Coast Framework identifies as a focus area, Woodcore has been contracted to operate the Fukushima Laminated-Timber Advanced Manufacturing Center (FLAM), which was opened by the Namie government, and is the most advanced facility of its type in Japan.
A type of engineered timber, glulam is manufactured by sandwiching, joining, and bonding multiple layers of wood. Woodcore concentrates on manufacturing thick laminated timber products for use in large wooden buildings. After it opened in October 2021, FLAM’s first project was supplying lumber for use in the Osaka Expo, producing the pillars and beams that support the Grand Ring.
Director Asada Hidehiro says, “It is an honor to be able to greet Expo visitors from around the world with timber from Fukushima, and show them just how we’ve recovered.”
FLAM’s laminate production facility is 60 meters wide and 240 meters long. (© Nippon.com)
Asada Timber CEO and Woodcore director, Asada Hidehiro. (© Nippon.com)
Leading Japanese Facility for Large Engineered Timber
FLAM is located in the Tanashio business park, on Namie’s Pacific coast. While the site had been earmarked by the Tōhoku Electric Power Company for a nuclear power station, after the Fukushima disaster, the utility donated the site to the Namie government.
The vast FLAM site seen from a nearby hill. (© Nippon.com)
Woodcore uses only Japanese timber, chiefly that from Fukushima, and performs every step of the process to turn logs into laminate itself. The facility can manufacture beams up to 12 meters long, 1.25 meters wide, and 24 centimeters thick. It is also the first facility in Japan to feature a high output, high-frequency press that bonds laminate in around 10 minutes—a process that would take over eight hours if relying on natural drying—thereby enabling mass production.
Thick laminated timber ready for shipping. (© Nippon.com)
A high-frequency press enables mass production. (© Nippon.com)
Asada explains: “While Asada Timber had expertise in lumber and in the production of thinner laminated timber, and strong ties to local businesses, Tōju Sangyō had experience with thicker laminates intended for structural purposes, and a large distribution network. By partnering, we’re now able to offer any conceivable timber product. However, rather than focusing on the residential market, which is highly competitive, our focus is on the thicker, high-added-value, engineered timber that is used for school gyms, commercial facilities, and other large buildings.”
The factory employs 50 staff. (© Nippon.com)
Keeping the Lumber Industry Alive
As he shows me around, Asada frequently remarks that local lumber industry must not be allowed to disappear. Fukushima Prefecture is ranked fourth in Japan for forest area, and Namie has a long involvement in forestry. Asada Timber was founded in 1912, which means that the 2011 quake and tsunami hit just before its hundredth anniversary. Asada’s family was forced to leave Namie after the nuclear accident, staying with his in-laws in Chiba for a month before renting accommodation in Tokyo.
Most lumber is sourced from within Fukushima: cedar from Tamura and larch from Minamiaizu. (© Nippon.com)
Thick, laminated structural timber has been used for the columns and beams in the building that houses the plant’s lumber facility. (© Nippon.com)
Two years after being forced to evacuate, Asada moved back to Fukushima, where he lived alone in an apartment—his family still in Tokyo—and worked a second job while aiming to restart his business. Wearing a radiation suit due to Namie’s location in the exclusion zone, Asada spent every spare moment tidying up the facility before a very low-key reopening in 2014. Due to the stigma associated with radioactive fallout, the business did not bounce back to its former glory. It could not use timber from the Namie region, which had yet to be decontaminated, and that meant there were no buyers for lumber sourced outside the area either.
“People told me that if we stocked timber products from Namie, it would affect sales of timber from surrounding areas as well,” says Asada.
Even now, at a time when there is less stigma around the issue, Asada Timber still targets the civil engineering sector—many members of the general public still worry about where their wood came from.
Woodcore uses cesium counters to measure the radioactivity of logs when they are delivered, and of finished timber products before they are shipped.
Asada says, “we measure the radiation levels of every log, applying a radiation limit that is several times more stringent than that used overseas. Even then, only a few logs per year are rejected.”
The production line incorporates cesium counters. (© Nippon.com)
Helping Japan’s Forests
Asada says emphatically, “Trees need to be harvested at the appropriate time, and new trees planted in their place.”
Older trees grow more slowly, therefore absorbing less carbon dioxide. Oversized trees are also more difficult to saw. In recent years, there has been interest in the fact that wooden buildings have a smaller carbon footprint than their reinforced-concrete and steel-framed counterparts. Rather than leaving forests untouched, we can do more to prevent global warming by repeatedly harvesting and planting trees.
Logs that are too large for standard saws are more labor-intensive to process. (© Nippon.com)
This is particularly true in Japan, where a whopping 25 million hectares, or two-thirds of total land area, is forest, a figure that continues to increase, mostly due to plantations. Over half of Japan’s plantations are more than 50 years old, and therefore due to be felled. In addition to fighting global warming, forests can also prevent landslides, floods, and droughts. This means that well-managed forests make everyone safer.
While people tend to associate cutting down trees with environmental destruction, Asada says proudly: “The appropriate utilization of trees is imperative in Japan and in Fukushima. Woodcore will continue to use its advanced processing technology to fight global warming.”
Wood pieces left behind during production, called offcuts, are turned into woodchips and fuel for dryers. (© Nippon.com)
Offcuts are burned to generate heat, which is sent along pipes to dryers. (© Nippon.com)
Reviving the Local Economy
The facility dispatched its last consignment of timber for use in the Grand Ring at the end of March. When we visited, however, the staff were busy working on an order for use in a different Expo building.
“After all the Expo work is finished, we want to help rebuild Namie. We can do our bit by boosting the forestry sector, thereby creating jobs. The town’s population is increasing gradually, but residents these days tend to live alone—you don’t see many children. It would be nice if this went back to being the kind of place where you saw children playing after school,” says Asada.
The Namie government launched a project to redevelop the railway station precinct in autumn 2024. The government’s development proposal makes extensive use of timber. In addition to supermarkets and other commercial premises, as well as community spaces, the plan also includes large-scale public and private community housing. Little by little, we can expect to see children playing here again.
The proposed design for the Namie Station precinct. (Courtesy Namie government; © Kengo Kuma and Associates)
Laminated timber manufactured in Namie and lumber from Fukushima will be used for benches, signs, other street infrastructure, and other public-facing locations. While Woodcore has not officially won the contract, there are hopes that it will have a role in the project.
“The old Namie is gone forever, and we will never see everyone who lived here in the past returning. However, the town has got a lot of new things, to an extent that would have been unimaginable before the disaster. That is precisely why I want the government to make this somewhere that is impressive, even for overseas visitors, and somewhere that serves as a model for other reconstruction projects,” says Asada.
When the station precinct redevelopment is completed at the end of fiscal 2026, domestic and international visitors to Namie Station will be greeted by timber from Fukushima.
Asada said emphatically at the end of his interview that he wanted Namie to be a happening place again. (© Nippon.com)
(Originally published in Japanese. Banner photo: The nearly complete Grand Ring, viewed from Sakishima Cosmo Tower. © Hashino Yukinori of Nippon.com.)