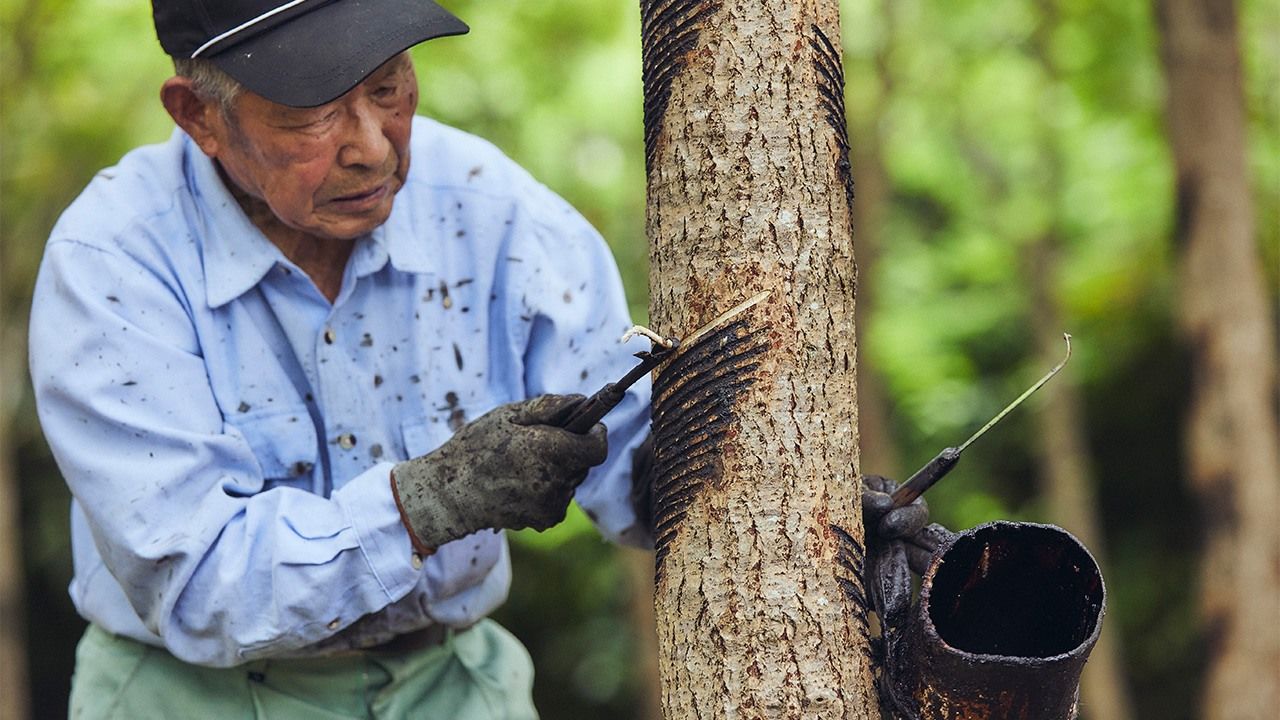
“Cool Traditions” Stay in Tune with Modern Life
Daigo Urushi: Japan’s Top Lacquer and the History of Its Art
Culture History- English
- 日本語
- 简体字
- 繁體字
- Français
- Español
- العربية
- Русский
A Decade for a Cupful
Urushi is traditional Japanese lacquer refined from the sap of Toxicodendron vernicifluum, known as the Japanese lacquer tree. Hardened urushi has strong adhesive properties and is also excellent at resisting water and fire. To collect raw sap for making the lacquer, harvesters make several horizontal cuts in the bark of a tree, then scrape off the sap the tree releases to seal the cuts. It takes 10 years for the tree to grow enough for sap harvesting, and only 180 grams, or about a cupful, of sap can be harvested. Each tree can only be harvested once, and never again. To the harvesters, this makes lacquer immensely valuable, giving rise to the saying, “Every drop of urushi is a drop of blood.”
A wooden urushi oke bucket (left) used to hold the harvested sap that is lacquer’s raw material. Once wood particles are removed, the material is called kiurushi (raw lacquer), which is whipped into a homogenous mixture in a process called nayashi. After the kurome process of heating and evaporating moisture content, it becomes translucent, viscous, refined urushi lacquer.
The history of urushi is long, and lacquered vessels have been recovered from Jōmon sites dating back over 10,000 years. During the Asuka (593–710) and Nara (710–94) periods, urushi was used for buildings such as temples, as well as for sacred Buddhist tools. The lacquerware industry flourished during the Kamakura (1185–1333) and Muromachi (1333–1568) periods, and urushi was used on the tableware of nobles and warriors’ armor. In the Edo period (1603–1868), famous lacquer centers gave birth to traditions like Wajimanuri or Aizunuri lacquerware, and such vessels became a prized export commodity. There was even an urushi display space in Marie Antoinette’s room in the palace at Versailles. Japanese lacquerware became loved by European aristocracy, and the name “japan” was used synonymously for it, much as “china” became synonymous for porcelain, as both were representative crafts of East Asia.
Lord Kōmon and the Spread of Urushi Trees
Daigo Urushi is rich in urushiol, a phenolic compound. The higher the urushiol content of a sap, the more transparent it will become as finished urushi. Daigo Urushi is also prized in Japan and abroad for its unique luster, which gives pieces a sense of depth and warmth when applied as a topcoat. Thus, this high-quality lacquer has long been used for finishing coats on top-end urushi wares like Wajimanuri. Urushi artisan Ōnishi Isao, a living national treasure, is one ardent fan of Daigo Urushi, saying, “Layering coat after coat gives a luster with ever greater depth. It’s very difficult to get that sheen with any other material.”
Daigo Urushi is a name used for the lacquer from sap harvested around the towns of Daigo in Ibaraki Prefecture and Nakagawa in Tochigi Prefecture. The harsh cold of the winters around Daigo is ideal for urushi production, and it has long been known for the quality of its lacquer. People have been growing the source trees there for centuries, dating back to when Tokugawa Mitsukuni (1628–1701), second lord of the local Mito domain—and famed now as the inspiration for the television character Lord Kōmon—encouraged their cultivation. He had farmers plant one tree for every koku (a traditional measure equaling around 180 liters) of rice their land could produce. At the time, the trees were also used to produce candle wax. In the early Meiji era (1868–1912), production reached around three metric tons annually, and from the early Shōwa era (1926–89), urushi harvesters would come from other prefectures like Fukui, Ishikawa, and Fukushima to gather sap around Daigo and Nakagawa.
While this area was once Japan’s leading lacquer producer, Ibaraki is now second and Tochigi is third, after first-place Iwate Prefecture. Iwate has taken the lead because of the concentration of harvesters in the Jōbōji district of Ninohe, the center for Jōbōji Urushi production.
The Decline of Domestic Lacquer
As cheaper lacquer from China and elsewhere has become more common, Japanese production has started to decline. There were once over 150 expert harvesters when the industry was at its peak, but with their advancing age, that number has dwindled, and today only a few are left. Urushi harvester Tobita Yūzō saw the danger in this, and in 2010 worked with the Daigo municipal agriculture and forestry department to establish the Daigo Lacquer Preservation Society, made up of 10 harvesters in the Daigo and Nakagawa area. At the same time, the group also decided to absorb the various names once used for local lacquer, such as Okukuji Urushi or Ibaraki Urushi, under the Daigo Urushi name due to its historical and cultural importance. As of 2023, the society now has 18 members, with young men and women in their twenties joining and working actively.
The Preservation Society has two primary activities. The first is to actively promote urushi tree cultivation to increase production. The practice once focused on hillside planting, but now they plant on the flat for easier management. The second is to train successors. Veteran harvester artisans devote valuable time without reservation to passing on their skills, teaching younger people how to cultivate seedlings, transplant trees, prune branches, cut underbrush, manage fertilizer, harvest sap, and fell old trees.
Japan’s urushi crafts have over 1,000 years of history. However, 98% of the basic material supply, the lacquer, is based on imports from China and elsewhere. Japan’s lacquer production is dwindling every year, and the skilled harvesters’ number is declining as well. One reason for this is the relatively low income for the work compared to the time and effort required for harvesting, as well as the availability of cheap, lower quality, imported lacquer. Given that background, it is quite important that the Agency for Cultural Affairs announced in 2015 that only domestic lacquer should be used in the preservation and restoration of national treasures or important cultural assets. This has made Daigo Urushi all the more vital as a resource for restoring such important cultural properties as the main hall at the Kyoto temple Chion’in. This drives home the issue that securing superior quality materials is an urgent issue in preserving Japan’s traditional culture.
Nidaira Yoshihiro, head of the Daigo Lacquer Preservation Society (right), and the first society head Tobita Yūzō.
(Originally published in Japanese. Banner photo: Expert harvester Tobita Yūzō collecting sap for urushi. All photos © Otome Kaita.)