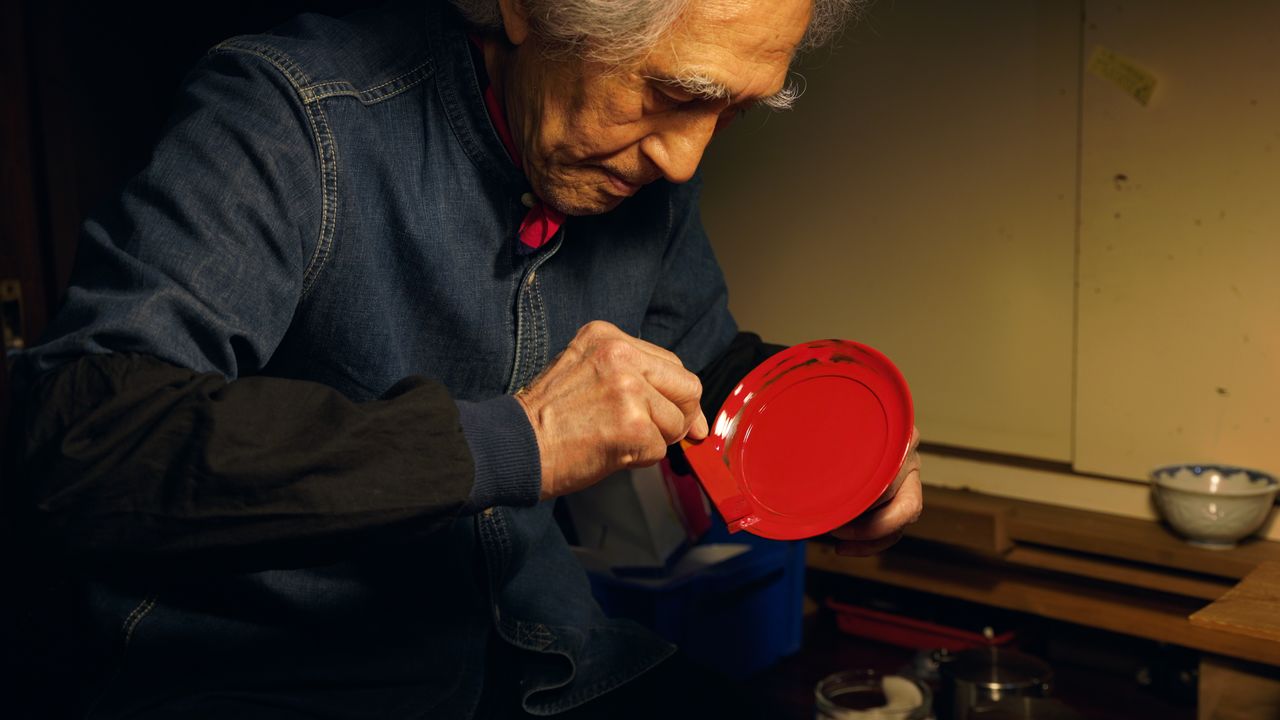
The Sap of Life: Harvesting Lacquer for Japan’s Top Artisan
Culture History- English
- 日本語
- 简体字
- 繁體字
- Français
- Español
- العربية
- Русский
Ōnishi Isao is a living national treasure—officially, he has been designated a preserver of important intangible cultural properties for his work in the kyūshitsu lacquerware style. Kyūshitsu is a particular style of lacquerware that consists only of painting layers of lacquer with a brush without other decoration, as opposed to inlaying pieces of mother-of-pearl and other seashells for raden, or applying gold over painted lacquer as in makie. Ōnishi uses Daigo Urushi, considered the pinnacle of Japan’s lacquer.
To collect lacquer, first the harvester makes a cut about five millimeters deep in an urushi tree’s bark. Then, gradually longer cuts are made at regular intervals above that. The tree naturally sends sap to try and fill those cuts, and the droplets of sap scraped from those cuts are the raw material for urushi. No sap can be collected below the third or fourth cut from the bottom. Doing so would interfere with the sap’s flow. Harvesters scrape the sap collecting in the fifth and higher cuts with a sickle, putting it into a collection bucket.
Sap collecting in cuts in the tree bark.
Urushi collection starts in early June each year, and the season ends at the end of October. The sap collected until early July is called hatsuurushi (first lacquer) and is used for roiro migaki, the final polishing stage to bring out luster. The next batch, gathered in the hot season from mid-July to mid-August, is called sakariurushi, considered the highest quality of Daigo Urushi. The lacquer that Ōnishi uses in his final layering stage is this incredibly valuable lacquer of supreme transparency. The video shows sakariurushi being collected. Later sap is called osourushi (late lacquer) and then urameurushi (back lacquer), which are used for middle or lower coats.
Ōnishi lets the base urushi he receives from the harvesters sit for two or three years so the water content can gradually evaporate for greater viscosity. He then chooses a particularly hot summer day to put the aged urushi in a wooden bowl to sit in the sun at around 40°C while he stirs it with a large stick. This process distributes the lacquer to increase uniformity and helps evaporate more water. This kind of refining is usually done at a lacquer refiner’s workshop, but Ōnishi prefers to do it himself.
He adds pigments, like red or green, to the refined lacquer and mixes it with a paddle or stick to create colored urushi. He then leaves it to sit a few days more so the pigments can blend completely with the urushi, and strains the mixture through washi paper to remove impurities. After this multistage process, the colored lacquer used for topcoats over the base and middle coats is complete.
Pigment is kneaded in with a wooden stick for even distribution through the colored lacquer.
Most urushi vessels made in Japan’s famous lacquerware centers use commercially available colored lacquer from a tube, so it is incredibly rare for an artisan to create it entirely by hand from the base sap. “They call me a living national treasure, but I’m just a craftsman,” Ōnishi insists. “I try not to leave anything up to anyone else. I try to finish each step of the process with care.”
The core of Ōnishi’s craft is how he approaches these priceless tree-born “droplets of life” with all his body and soul, and the reason he is a living national treasure in truth.
A lacquerware piece by Ōnishi Isao. He does more than just apply the lacquer; he also shapes the base vessel. Most lacquerware producers break up that labor, but Ōnishi does everything himself. This piece was made from nearly 100 thin layers shaped using the magewa technique of steam-bending wood. Most producers use joinery or lathing techniques to form vessels, but this bending process allows the wood in Ōnishi’s pieces to breathe more actively and last for centuries.
(Originally published in Japanese. Text by Kondō Hisashi of Nippon.com. Video and photos © Otome Kaita. Banner photo: Ōnishi Isao painting a Daigo Urushi topcoat.)